Why Homes Aren’t Built Like Cars but Should Be
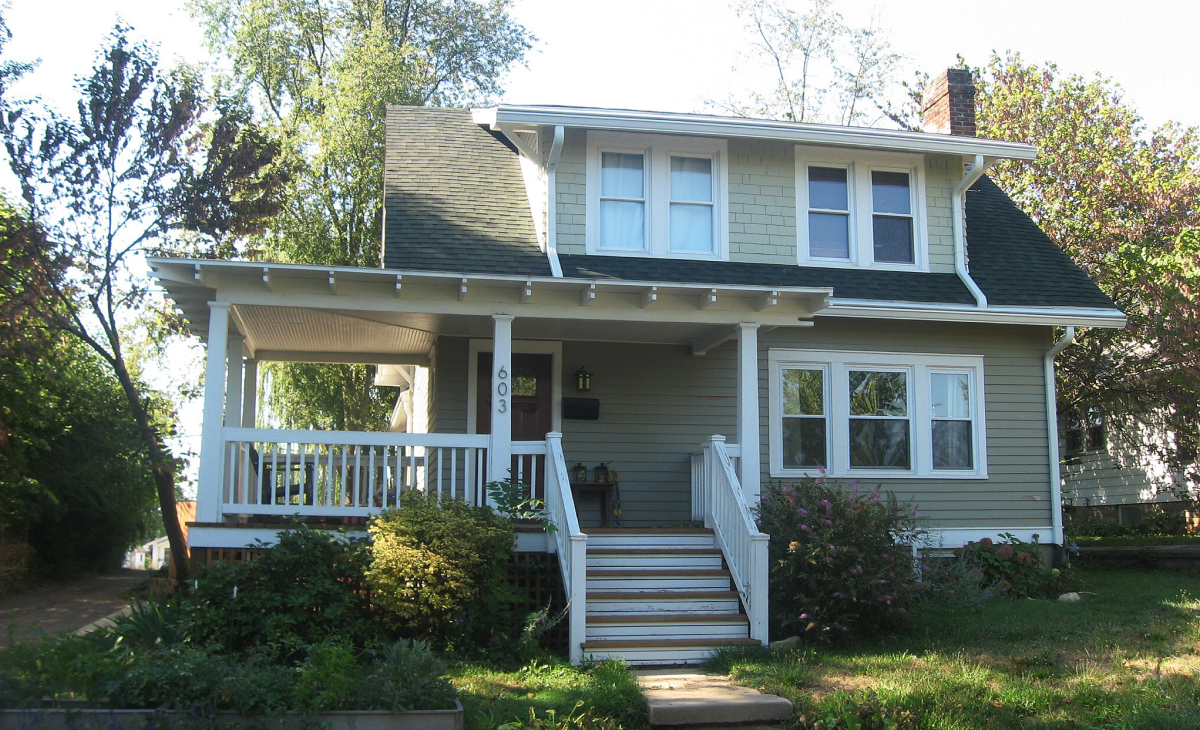
Factory-perfect homes have a long history in the U.S.
If there’s one thing homeowners and contractors can agree upon, it’s that traditional homebuilding is — dare we say it — inefficient.
The average single-family home takes about seven months to complete. Compare that to a Tesla factory, which churns out a super in-demand electric vehicle every 56 seconds.
Why is the industry so stuck? Depends on whom you ask. Theories include burgeoning safety regulations and paperwork, wariness of new technology, architect and contractor conflicts, lengthy bidding processes, and shortages in labor and materials.
Modular housing can shorten the process, but it’s had a mixed track record here in the States. It helps to look at a couple of previous examples to understand why.
Sears Modern Homes
Back in its day, Sears, Roebuck and Company was a retail juggernaut. An Amazon before there was an Amazon. Their catalog (and goods) reached homes all across the country for 20 years before they had the bright idea to sell new homes themselves.
From 1908 to 1942, Sears sold over 70,000 kits through its Modern Homes catalog. They weren’t the first company to offer prefab housing at the time, but they were the largest, and Sear’s solid reputation gave the company a leg up in this new venture.
Sears made upwards of 370 designs in all sorts of architectural styles, many featuring new technologies like electricity, central heating, and indoor plumbing. The first homes carried an upper price tag of $2,890, or around $93K in today’s coin.
Customers received the materials by railroad boxcar and built their homes with the help of friends and family, local builders, or Sears’ own construction services.
The kits, which included over 30,000 parts and weighed about 25 tons, used lumber and balloon-style framing systems that required only one carpenter. The homes were (and still are) considered well-designed and constructed, and were massively influential on architectural styles and the growth of the suburbs.
Sears soon threw in mortgage loans with easy terms, and their applications omitted questions about race or ethnicity, making a slice of the American dream available to a wider selection of the country, including the influx of immigrants in the early 1900s.
But the loans were discontinued in 1933, during the Great Depression, which forced Sears to liquidate $11 million in defaulted debt. Between this and national restrictions on building materials due to WWII, Sears discontinued its Modern Homes program in 1942.
Lustron Houses
Let’s skip a few years ahead, to post-WWII, when our soldiers found a lack of housing upon their return. As part of the New Deal, President Truman granted over $12 million in 1947 to the Lustron Corporation to fix the problem with large-scale prefabricated housing.
The houses, which featured porcelain-finished steel panels, came in three basic models. They could be built in about two weeks, and had an initial price tag of about $9,000 each, or $123K in today’s cash. Not bad, as this was 25 percent lower than comparable conventional housing.
But Lustron would build only 2,500 homes, far below the promised total of 45,000, and they declared bankruptcy in 1950, within three years of breaking ground.
What went wrong? Observers point to Lustron’s faulty distribution strategy, production delays, and the skyrocketing cost of steel, all of which jacked up the prices beyond what homeowners wanted to pay, and construction times beyond what they could endure.
But Sears and Lustron had made their mark. One estimate is that 70% of the Sears’ homes are still standing, thanks in part to their resilient materials. And about 1,500 Lustron Homes remain today, their steel structures enduring the test of time.
A lasting foundation
Homes from both ventures are honored on the National Register of Historic Places, and admired by fans today.
While neither Sears or Lustron achieved enduring success, it’s inaccurate to call the efforts failures.
They were just ideas ahead of their time.
Cheers,
Mike
Mike McAllister is a writer specializing in future-ready home construction. He lives in Los Angeles.
Track the global transition to sustainable homebuilding.
Subscribe to the Momo Focus newsletter.