Dwellings Demystified: From Prefab to Modular to Panelized
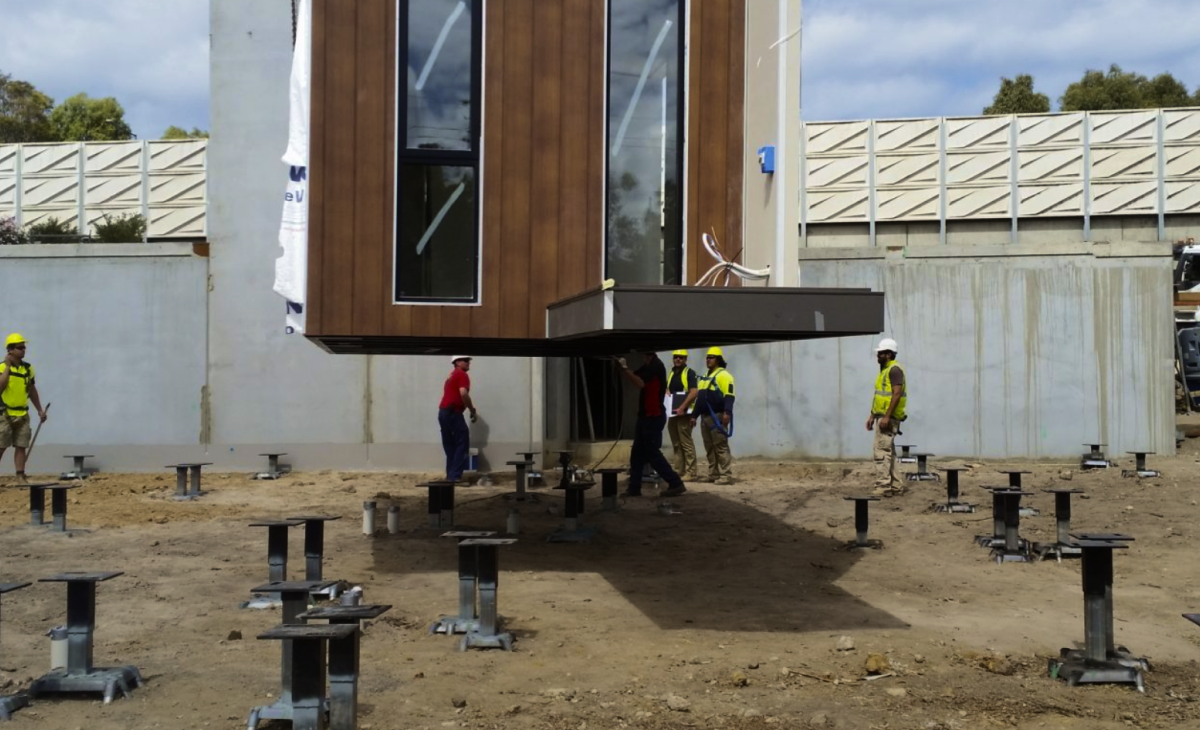
Like any industry, homebuilding is full of terms that can confuse newcomers (“balusters,” anyone?). We want to untangle it all for first-time buyers (and everyone else, too).
After all, in terms of importance, a home is way up near the top of the list of lifetime buys. It should be a fun choice to make, not a mystery to solve.
Since demolition is a blast (dad joke, sorry), let’s break down the differences between manufactured, prefabricated, modular, and panelized homes.
Manufactured
You know these as mobile homes.
They’re built entirely in a factory and transported to the site as a complete unit, so no construction is done onsite.
They’re shipped on their own wheels (you’ve probably been stuck behind one on an interstate or two), then laid on concrete slabs or a crawlspace.
Sometimes they don’t even strip the wheels. They just cover them up with a skirt (which doesn’t really fool anyone).
Manufactured homes are inexpensive and easy to build, but they age quickly, have low resale value, and generally don’t fare well in tornados.
Prefab
Prefabricated, or prefab, is more of an umbrella term that includes both modular and panelized homes. Think of prefabs as automobiles, and modular and panelized as sedans and sports cars.
Prefabs are built off-site in a factory setting. They’re constructed in sections or modules that are later transported to the building site for final assembly.
Prefab housing generates far less waste than traditional homebuilding, so it’s easier on the environment.
By manufacturing the structural elements of prefab in the factory, contractors also eliminate many of the on-site delays that crop up in traditional construction.
Contractors can use smaller crews of laborers with less specialized skills, too, so they’re easier to find in a tight job market.
The pre-made elements can also be built in the factory with much greater precision than in traditional homebuilding. That all adds up to a faster, less expensive, and safer build process.
Modular
These consist of multiple box-like modules constructed in a factory, from the studs to the paint. The boxes get transported to the construction site and put together like puzzle pieces to create the final home.
The boxes can be configured and combined in a bunch of different ways, allowing for flexible floor plans and customization. Like the other home types on this list, modulars offer a faster construction timeline compared to traditional site-built homes.
But the bulky shape of the boxes means transportation costs can add up, and customization options are more limited than in panelization.
Panelized
Like their modular cousins, panelized homes are built with sections pre-made in a controlled factory setting.
Compared to modular boxes, panelized sections are flatter in shape and more stackable, so they’re easier and cheaper to transport.
Another big difference is that with modular homes, the boxes are built entirely in the factory, including finishing touches like paint and flooring. With panelization, the sections can be finished onsite.
That means homeowners get more customization options, with design flexibility around paint, hardware, and luxury details.
Panelized homes are also faster to build than modular homes, which can take about 3-6 months to construct. Some panelized homes, by contrast, can be built in a matter of weeks.
A next-gen choice in housing
Here at Momo, we build panelized (what we sometimes call “quick-build”) homes with all the features named above.
Our crack team of architects, engineers, and designers get everything right ahead of time, so the build is safe and fast.
Because our panels are created with cold-formed steel, they stand up better than mobile homes to tornados. And we think our homes have way better curb appeal, too (without the skirts).
Homebuyers—we’re here to make your choices clearer.
Hope this helps.
Cheers,
Mike
Mike McAllister is head of story for Momo Homes.
Track the global transition to sustainable homebuilding.
Subscribe to the Momo Focus newsletter.