Reinventing the homebuilding supply chain
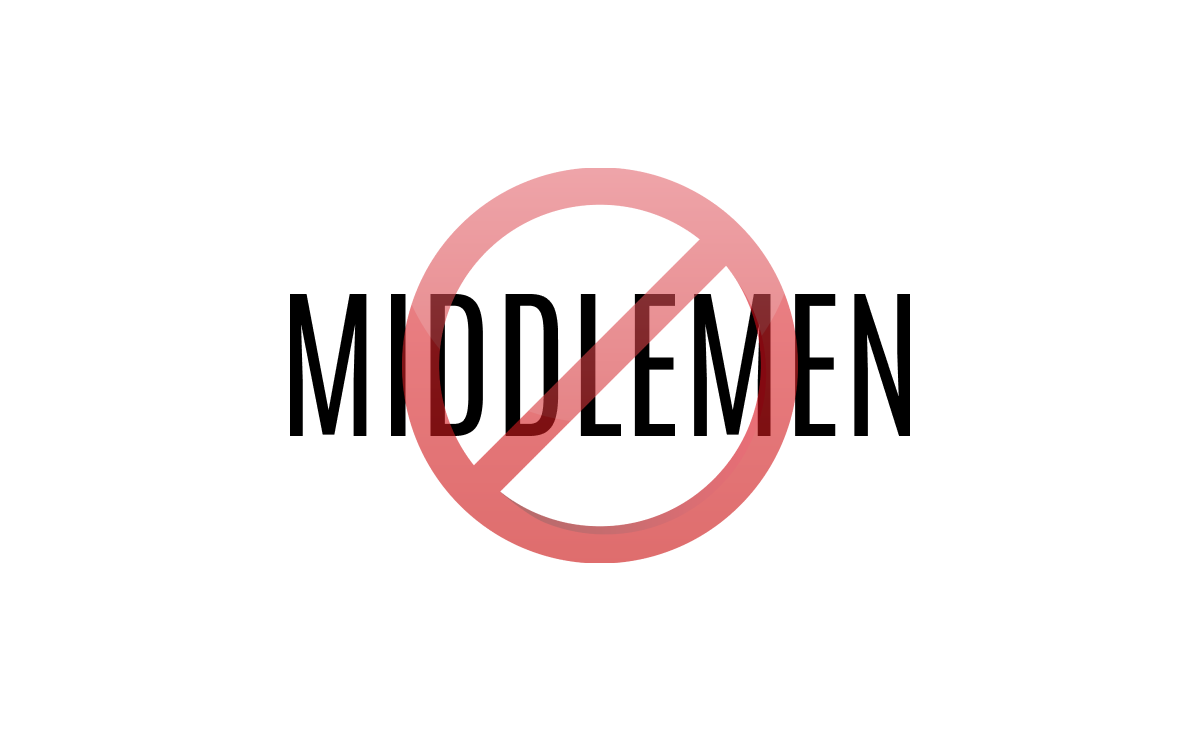
Builders and contractors know all about middlemen.
Getting construction materials to a job site can involve a slew of them. The old-school sourcing model depends upon a long string of third parties. Stuff goes from supplier to broker, a broker through an intermediary, and on and on until it (hopefully) arrives onsite.
Builders get caught in the middle
It’s a system that bogs down builders too often with delays, paperwork, financial terms, waste, and inefficiency. And with each third party slapping on their markup, we can throw “costly” in there, too.
Sometimes those middlemen start out by offering a convenient service (hello, big-box stores and online retailers) but eventually get a bit profit-crazy, growing big, unwieldy, and ever-more power-hungry. This makes the whole process more fragile and prone to inequality.
What’s more, the homebuilding supply chain is vulnerable to external factors, like global pandemics, port bottlenecks, and the Russo-Ukrainian war. Which is all happening when the demand for single-family homes is skyrocketing.
A supply chain built for the future
Modular, panelized, or quick-build homes (they’re variations on a theme) solve many of these problems by reworking the homebuilding supply chain.
Panelized homes are made from components manufactured in climate-controlled factories. The components are then shipped to the jobsite and assembled by a small crew of non-specialized workers.
This all makes for a faster, safer, less costly, and more sustainable homebuilding process. With benefits like these, one supply chain advisory group predicts that, “Modular construction is the future of supply chain.”
We’re aiming even higher: Quick-build construction is the future of homebuilding.
We’re achieving that future partly through our own approach to distribution. We call it a vertically integrated direct-to-builder supply chain. A three-step system that lets builders go from lot to lockup in three weeks.
Here’s how it works:
1. Sourcing in Asia
We source from the best manufacturers and factories in Asia, where we have decades of experience.
Asia is the primary source of all construction materials in the United States, but we skip the middlemen and ship precision-engineered home components directly to the builder’s jobsite for less cost.
2. Pre-assembly in Panama
Move over, Portugal. Panama is now the number one destination for Americans retiring abroad. The country is peaceful, prosperous, and economically sophisticated.
By locating our factory in Panama, we can save on the time and cost of handling shipping containers. Plus there’s the handy favorable trade relationship Panama maintains with the United States. (We pass these savings on to builders, of course.)
We build all our products to exceed US standards for quality and endure rigorous testing, which we document and make available for review.
3. Buildout at the jobsite
Our precision manufacturing process lets builders work fast with a small, nonspecialist team. Here’s how the build works:
- Guidance: A Momo Homes primary builder and team will be on-site providing expertise and answering questions the week of the builder’s first home.
- Foundation: The Surefoot foundation is installed, with footings that are job-specific, designed for the soil conditions of each site, usable on a wide range of projects, and meet all compliance and regulations.
- Framing: The Frame and exterior components arrive in shipping containers, which hold wall sections housed in cassettes, and include the good stuff like insulation, doors, windows, siding, and flooring.
- Assembly: Walls are pre-assembled at our manufacturing plant using our “easy handle system” and packed into shipping cassettes. The unloading and assembly process is designed to enable two nonspecialists to assemble walls in fewer than three days.
- Interiors: Components typically arrive seven days after the walls and include cabinets, bathrooms, kitchens, flooring, luxury components, and more.
- Lockup: The work finished by the builder includes: drywall, paint, electrical, plumbing, water hookup, and heating and air conditioning.
One, two, three. Fewer steps mean fewer stoppages. And more savings for builders.
Cheers,
Mike
Mike McAllister is head of story for Momo Homes.
Track the global transition to sustainable homebuilding.
Subscribe to the Momo Focus newsletter.