Can panelization solve the housing crisis?
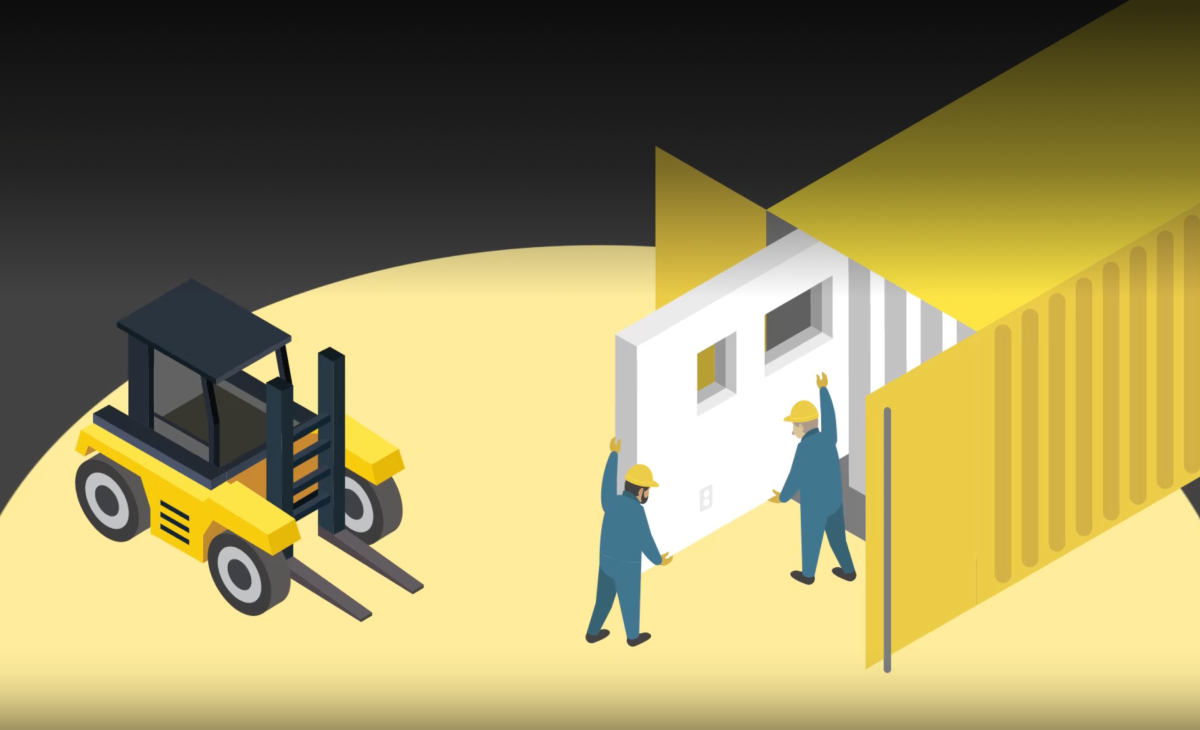
Let’s cut to the chase: traditional homebuilding is broken.
Like stick-built construction debris, the evidence has been piling up for years.
From blueprint to inspection, each traditional home is built like a one-off prototype, making for an unpredictable and long construction process.
Last year, the average home took at least eight months to build.
Costly, too. Though the prices of construction materials stabilized a bit after the pandemic, signs point to more volatile swings in supply and pricing and further rising costs in 2023.
Home construction is done mostly by hand, by an expensive labor force, using nail guns and two-by-fours. What’s worse, the labor outlook is also bleak, with the workforce shortage topping half a million workers in 2023.
All of this contributes to a serious problem. Depending on the source, the country is short anywhere from 1.5 million to 6 million homes.
What’s more, a recent study by The National Association of Realtors and Realtor.com found that middle-income buyers face the worst shortage of affordable housing, with the market short a good 300,000 homes.
How about something hopeful?
Right about now you’re probably thinking, Great, thanks for the list of depressing stats.
You’re right, which is why we humbly offer one solid answer to the current problems of housing: panelized homes.
Panelized homes are made from components manufactured in climate-controlled factories. The components are then shipped to the jobsite and assembled by a small crew of non-specialized workers. This all makes for a faster, safer, less costly, and more sustainable homebuilding process.
Aren’t they boxy and cheap-looking?
Nope.
Today’s panelized homes come in a range of architectural styles that will fit gracefully within your chosen neighborhood. They offer plenty of customization options, too, with luxury fittings, modern color palettes, and cutting-edge appliances.
Why are they better than stick-built homes?
Let’s start with collaboration.
In traditional homebuilding, costly and time-sucking construction delays often crop up due to conflicts between the architect’s vision and the engineer’s need for things to actually work.
In panelization, engineers and architects and even interior designers often work together ahead of the project, fine-tuning the kinds of details that often bog down traditional builds at the job site. This close, pre-build collaboration produces designs that function well, homes that flow beautifully, and builds that cost way less.
What’s next, a factory for homes?
Actually, yes.
In traditional homebuilding, onsite construction can be knocked off schedule by any number of unpredictable factors, like El Niño rainfalls, broken cranes, or faulty measurements.
With precision-engineered components built in indoor facilities, panelization skips the uncertainty of sketchy weather patterns or flakey subcontractors.
Manufacturers of panelized homes can measure twice, cut once in a controlled setting. This means precision-engineered components that are guaranteed to assemble the right way, right away.
What about that labor shortage?
It takes an average of 22 subcontractors to build the traditional single-family home. That’s a lot of potential for miscommunication, mismatched skill levels, and no-shows that will flick the first domino in a long chain of delays.
Panelized homes can often be put up by much smaller crews of non-specialized laborers in a fraction of the time, for a streamlined, more affordable build.
But are they sustainable?
When it comes to carbon, nobody wants big feet. Modern panelization takes advantage of new technologies to deliver a more sustainable home with a smaller carbon footprint.
The controlled factory environment of the building process promotes efficient use of materials, minimizing waste and reducing onsite disruptions.
The precise measurements and tight construction tolerances of panelized homes mean greater energy efficiency and lower long-term operating costs. Many manufacturers of panelized homes go even further, offering homes with energy-efficient windows, appliances, and climate controls.
Can panelization save the world?
The jury’s still out, but the facts speak for themselves. The broken process of traditional homebuilding is ready for reinvention.
Cheers,
Mike
Mike McAllister is head of story for Momo Homes.
Track the global transition to sustainable homebuilding.
Subscribe to the Momo Focus newsletter.